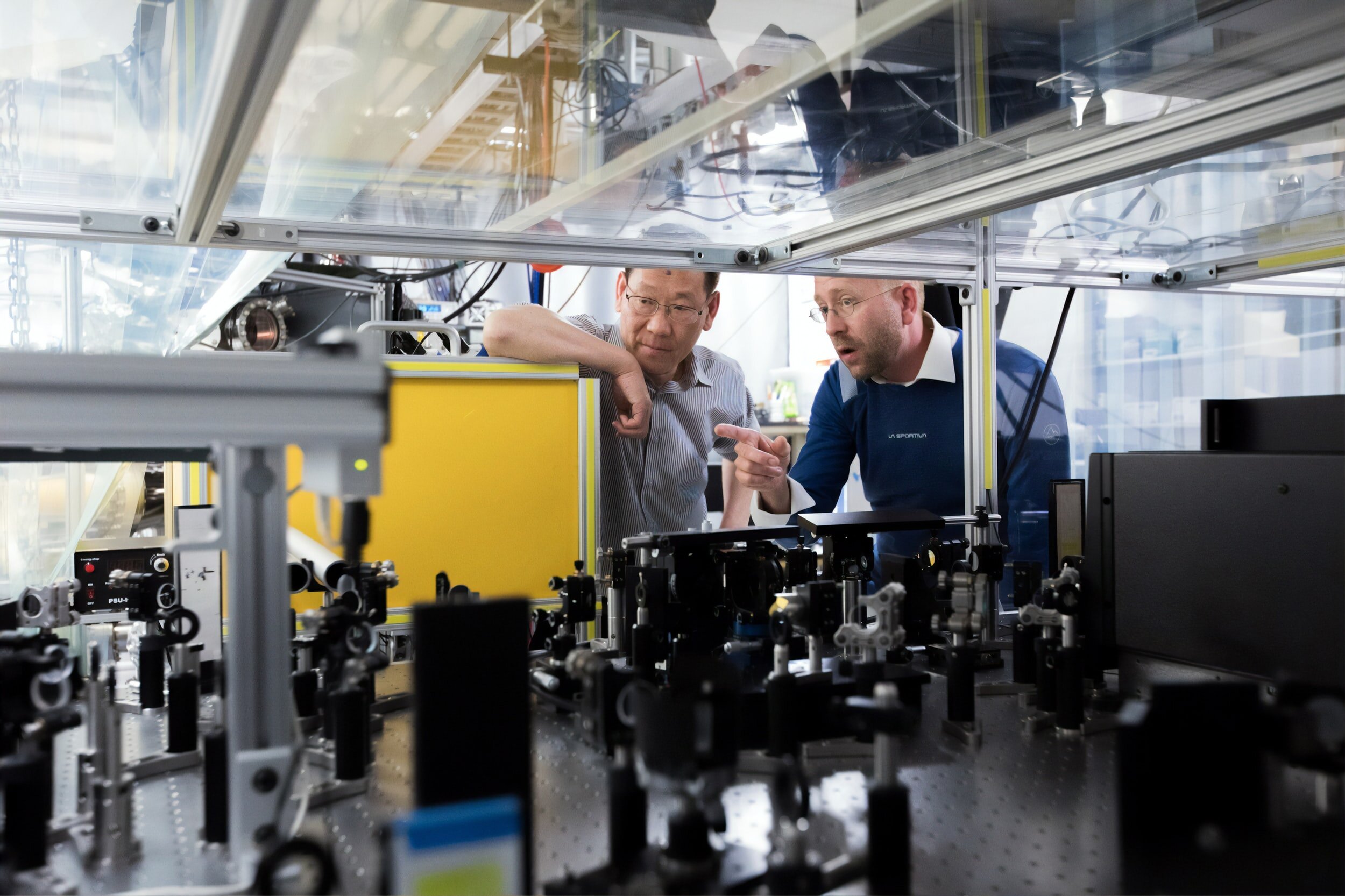
Sourcing Process
Assessing you requirements
The first step is to get an overview of your needs. What do you want to produce and what quantity? What are the product’s technical specifications? What is the expected standard and quality?
Collecting supplier bids
We create a requirement sheet and send it to our extensive network of suppliers. We work with ground level factories that have more competitive prices than suppliers on online platforms many of whom are traders claiming to be factories. We review the bids and grade the suppliers based on their expertise, market knowledge, capacity, financials and ultimately price points and quality.
Suppliers background check
We will do a background check on the chosen suppliers, making sure they have all the business licenses and certificates. We use our access to government databases and third parties to ensure the credibility and history of the factory.
We send you a quotation
We provide you with a quotation from at least 2 suppliers, to make sure you are getting the best option relative to your requirements. We also provide you with the contact, name and address and any relative information in all transparency in a pdf file.
Factory audit report
When you accept the quotation, we do a factory audit. We give special attention to: Attitude, Size, Specific Machines, Environment, Social responsibility, Documentation, Process Control and Management Structure. During the visit, we also make sure to clearly communicate your requirements and expectations. We provide you with a detailed report to make a final decision.
Ordering samples
Once the factory is approved, we do a sample production. We review key points with the supplier such as appearance, critical dimensions, critical areas and performance. We inspect the sample in our offices, and we will then send you the sample and a full pdf report.
Production management
Your Ausino project manager settles an agreement (detailed proforma invoice and sales contract in both English and Chinese) with you to make sure that all requirements are understood and accepted by all parties. Our purchasing team handles all the order management in China and follow up tasks with the factories and the shipping company.
Quality control
As part of our service, we do a range of quality control inspections as appropriate on site – dupro inspection, final inspection and loading inspection – to give our client’s visibility of the products before shipment. This means that you can see the products and decide to ship with confidence.
Shipping management
We send you the best shipping quotations according to a wide array of conditions: your desired schedule, your budget, the merchandise volume, the number of containers, the number of factories, the packing of the goods, the incoterms, the necessary tests and certificates. You receive quotations from internationally established forwarders.
Always at your service.
You receive status & schedule updates by automatic emails. At the same time, your Ausino account manager remains available for any question.
Our service starts when you ask for a quotation and continues after you receive the goods. If you have any claim, our sales team remain at your disposal to take care of any after sales issue.
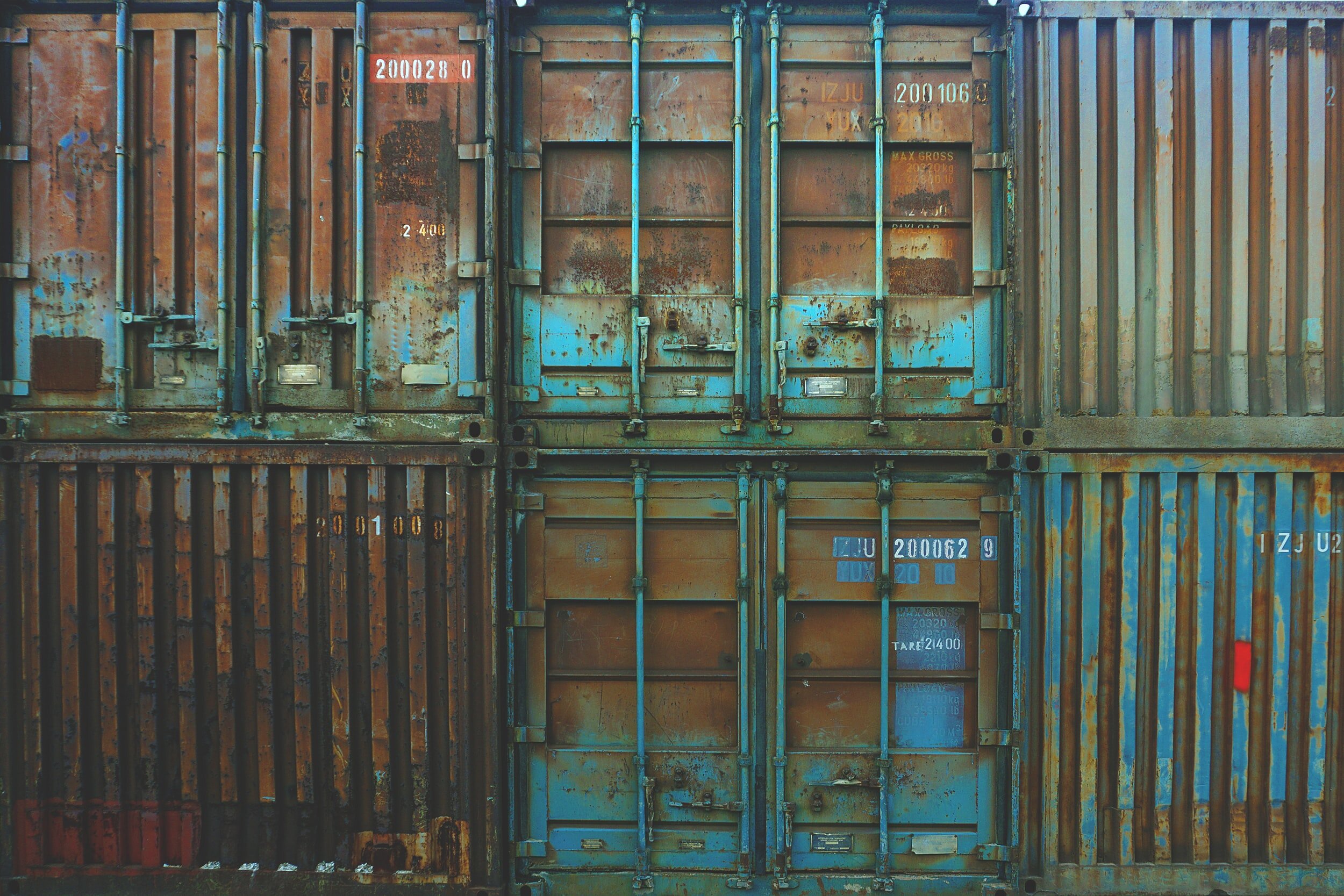